Context
ISERCO intervened within the framework of the optimization of the conveying lines of a large sugar group. The objective was to optimize the production at the end of the shift of the operators in charge of the sugar conditioning.
ISERCO’s work is to integrate solutions for transferring, dosing, weighing, or packaging powders, through a range adapted to silos, Big Bags, and bags. The products proposed by the company evolve according to the needs of the customers and the requirements imposed in the various industries. Each piece of equipment is designed to guarantee ergonomic conditioning or deconditioning of Big Bags and to allow easier and safer handling for the operator.
ISERCO’s customer’s activity is the manufacture of sugar in calibrated pieces as well as the boxing of the product. Within the framework of the modernization of a part of its production process, the industrialist wished to optimize the production at the time of the end of the shift of the operators in charge of the conditioning. At the end of the day, the sugar remaining on the conveyor line must be put in Big Bag so that it does not dry on the spot and does not take in mass. It can then be reintroduced into the production process. which limits any product waste.
The proposed solution
Before ISERCO’s intervention, the crushed sugar was first dumped into a wheeled cart and then transferred into a Big Bag by the operators using a shovel. To improve the process, ISERCO proposed a custom-made solution, which consists of a set of interdependent equipment. The system consists of a stainless steel roller crusher, a pneumatic conveying system, and an electrically operated big bag filling station with a buffer hopper. The big bag filling station is supplied with a steel frame.
Many constraints
One of the first constraints of the project was the location of the installation. The cart had to be easily maneuverable and compact because the space available on site was relatively small. This was due to the presence of a pillar close to the conditioning machine, and the limited space under the conveyor.
Secondly, the food industry is subject to strict sanitary regulations. The materials and surface treatment of the equipment had to be chosen according to these requirements. In addition, the equipment had to be easy to clean. Food certificates attesting to the compliance of the materials with food standards were also provided.
Another constraint was the various movements of the cart between four conveyor lines. Therefore, an easy connection to electricity was required.
Finally, to improve the process, the customer wanted the line to be able to operate completely autonomously. Once the cart was in place and the initial conditions were met, the operator could start emptying the conveyor and perform other tasks on the side without fear of sugar jamming in the machine.
The new conditioning process
From the conveyor to the Big Bag, the sugar passes through a set of several equipments connected by pneumatic transport. The sugar remaining on the conveyor is first diverted to a sliding plate equipped with a laser detector. The detection of the sugar on the plate allows starting the lump breaker installed on the cart. It also starts a pneumatic vibrating motor placed directly on the conveyor plate. The lump breaker is used to reduce the sugar into smaller pieces than originally. This is necessary to allow the product to pass through the pneumatic transport pipes without difficulty. The speed of the lump breaker is variable and is controlled from a variable speed drive located in a cabinet. The pneumatic transport is started by a vibrating bar level probe. Its sequence is automated and can be parameterized from an HMI (Human Machine Interface). The whole equipment is enclosed and has its own emergency stop to avoid any risk of an accident.
Then, the pneumatic transport transfers the crushed sugar to a Big Bag filling station located about ten meters from the conveying part. The product is discharged into a buffer hopper, allowing the sugar to be stored while awaiting conditioning. The detection of the high level of the buffer hopper is made by a vibrating bar level probe. Once this level is reached, the lump breaker of the cart and the pneumatic transport stop. The valve under the buffer hopper opens and the contents are emptied into a Big Bag. This Big Bag is put in place manually by the operator. The tightness is guaranteed by a pneumatic Clean Connect which is closed by HMI control. This system prevents any emission of fines and loss of product. It is also a “double skin” Clean Connect, allowing connection to a vacuum system. The detection of the high level in the Big Bag is done by microwave-level probes. Once the level is reached, the valve closes automatically. Finally, the Big Bag is evacuated using a pallet and a pallet puller. The contents of the Big Bag are then used for “remelting” and the production of new sugar cubes.
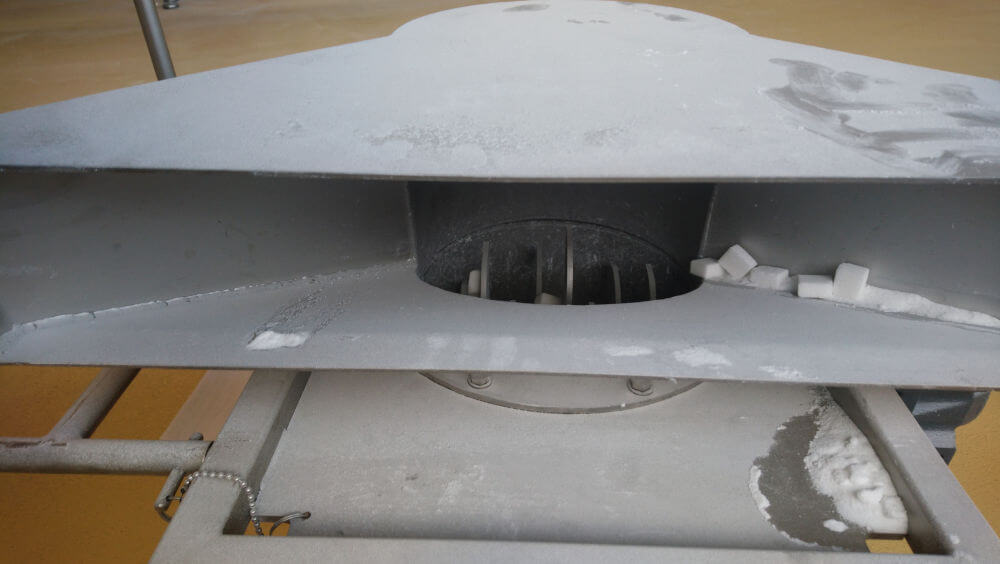
Bulk information
- Type of industry: Sugar
- Product : Sugar